Digital twin representation of an offshore wind turbine
The collective methodology of this work sought to address each component of the wind turbine in turn, first determining potential problems that could arise, for example the blade to develop cracks or the tower to corrode, then subsequently developing new monitoring solutions to mitigate part failure. The application of digital twin seeks to build on this approach by replicating all the constituent components of the wind turbine into a single digital model, thereby enabling real time monitoring of its entire structural condition.
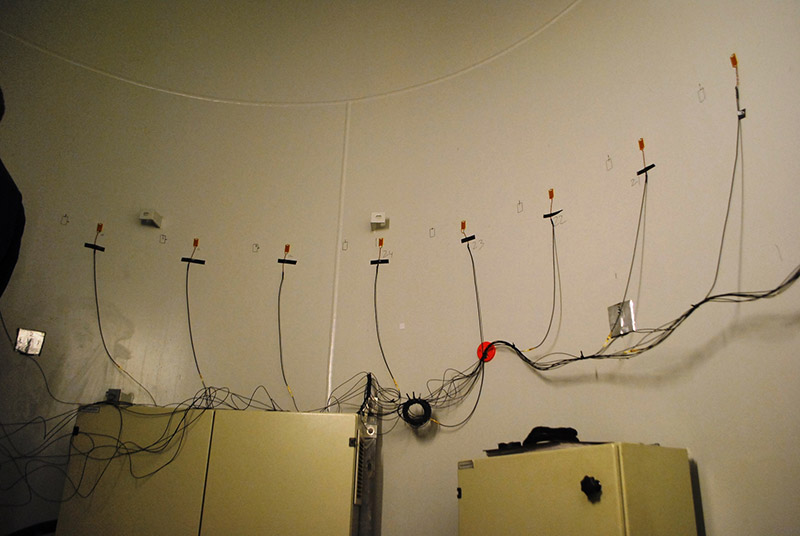
Data collection using guided wave inside a wind turbine tower
An offshore wind turbine typically consists of the nacelle (generator), blades, a foundation structure (piles/buckets, monopile/jacket), a transition piece and a tower. Experience shows that when problems occur they often arise from ageing, the main phenomena of which are: higher than expected levels of vibration leading to fatigue cracking in the support tower or loosening of flange bolts at its section ends; degradation of the grouted joint between the pile and transition piece; blades with cracking, damaged edges or erosion; and vibration related problems in the generator.
The wind turbine’s nacelle was the focus for the CMSWind project, the aims of which were to extend the lifetime and improve the operational efficiency of the generator’s rotating parts, and reduce noise levels emitted by the turbine machinery’s vibration. The approach used motor current signature analysis, operational modal analysis and acoustic emission techniques, together with vibration analysis, to monitor condition, enabling early detection of defects such as slip-ring corrosion and shaft/bearing misalignment. This led to improvements in the wind turbine’s overall operation, reliability and optimisation of its maintenance schedule.
Having identified that blade associated failures featured in a high percentage of wind turbine breakdowns and malfunctions recorded across the globe during the last six years, the Regional Growth Funded (RFG) project, WTBMonitor, was created to tackle the issue. It investigated the feasibility of applying in service, structural health monitoring using acoustic emissions (AE) to identify and monitor crack growth in wind turbine blades. The study confirmed that AE signals can be successfully extracted, filtered and classified, thereby demonstrating that AE can yield vital information to help reduce operational and maintenance costs, and ultimately potential failure, when incorporated into a viable, remote condition monitoring system.
TWI was able to apply research undertaken as part of the OPCOM project, into the potential for low frequency, ultrasonic guided waves to monitor large areas of offshore structures over the long term, to the monopile section of wind turbines. Structural integrity may be affected by both corrosion and fatigue cracking over their serviceable life, which is normally in excess of 20 years. The project scope involved developing tools and techniques for the complete examination and monitoring of very large diameter, tubular steel structural components which exist in large numbers in offshore installations. Design of sensor arrays capable of withstanding marine environments, long term environmental influences on the test data, and modelling of the influence of component geometry and condition on the test were all incorporated.
The TOWERPOWER project, currently in its final stages, is aimed at advancing and integrating inspection techniques to produce a system that is able to monitor the entire wind turbine structure. Relying on a network of sensors of various natures, such as guided waves and AE; amplifying electronics; and advanced signal processing algorithms, the TOWERPOWER system will enable self-learning of the normal behaviour “signature” of the wind turbine structure and detect any deviation from the initial record. Real-time wireless connectivity will allow the TOWERPOWER solution to monitor offshore wind turbine conditions from an onshore location, taking into account the unpredictable nature of offshore conditions. For operators, this means the length of time between inspections can be increased leading to reduced maintenance costs.
Building on the combined prior expertise gained from these and other collaborative projects, TWI is now embarking on a digital twin solution for the wind turbine industry, with the intention of forming a joint project with industrial partners to deliver a fully integrated approach to structural health monitoring for improved reliability of wind turbines. A condition monitoring system will encompass the entire physical wind turbine providing ongoing structural health analysis. Simultaneously, this will be mirrored virtually with the creation of a 3D model of the wind turbine in the form of a digital twin, including input from different sensors positioned across the physical entity, to continually feedback monitoring data. The output will be fully comprehensive, real-time assessment of the structural condition of individual wind turbine assets.
Tat-Hean Gan, Business Group Manager, Integrity Management at TWI said ‘Digital twin’s intelligent data processing capabity makes it an ideal platform for preventive and predictive maintenance of the wind turbine’s behaviour and condition. These virtual models or twins will combine mathematical models describing the physics of the turbine's operation, with sensor data collected and processed from real assets during real world operations” he explained. Adding “Wind farm operators will benefit from being able to predict structural failure and plan maintenance activities with greater accuracy, affording them more control, resulting in reduced maintenance costs and operational downtime during the wind turbine’s lifespan.”
For more information, please contact us.